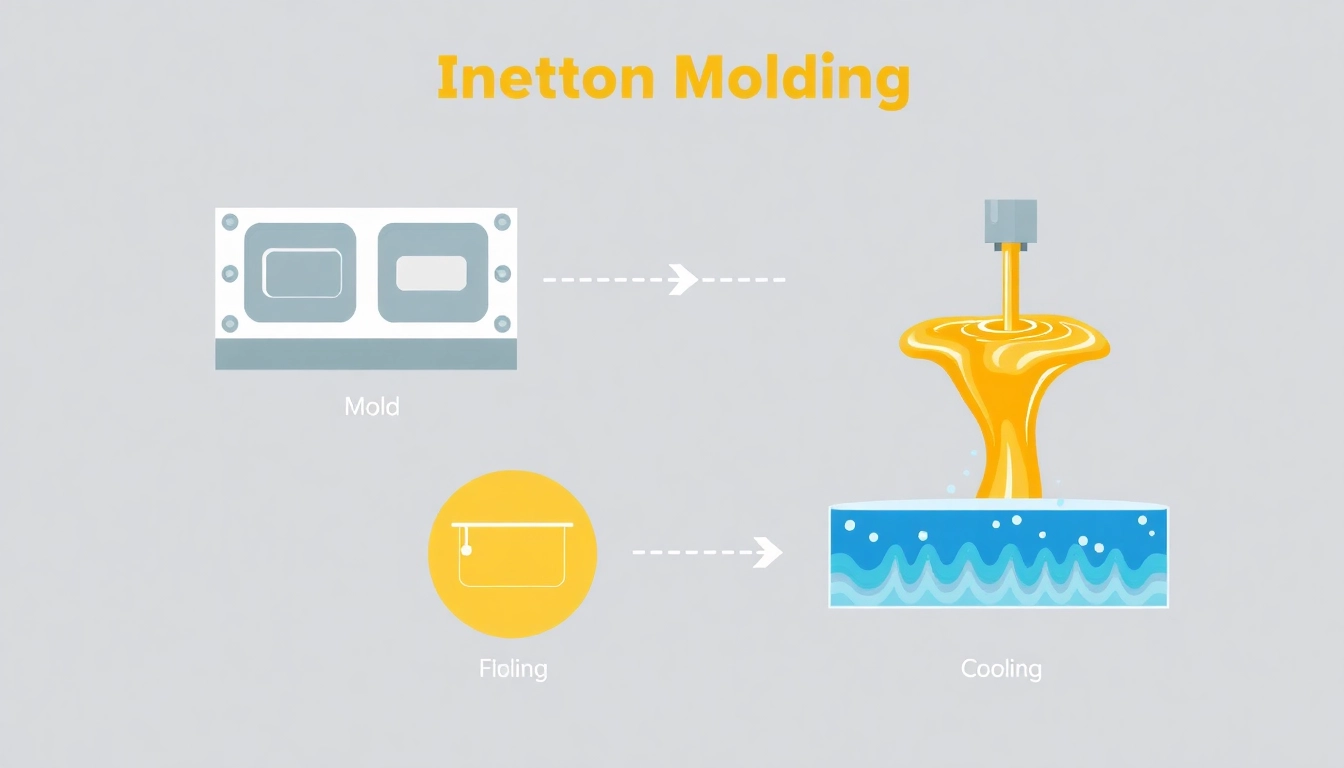
Understanding the Basics of Injection Molding
What is Injection Molding?
Injection molding is a manufacturing process that involves injecting molten material into a mold to create parts with highly accurate dimensions and complex geometries. Primarily used for producing plastic products, this technique is efficient for mass production, allowing manufacturers to produce thousands of identical items with minimal waste. The process begins when raw material—typically plastic granules—is heated until it becomes pliable, then injected into a pre-designed mold. Once cooled, the mold is opened, and the finished part is ejected. For more insights into the intricacies of injection molding, this article delves into its nuances, applications, and advantages.
History and Evolution of Injection Molding
The history of injection molding dates back to the mid-19th century with the creation of the first injection-molded item, a simple button created by John Wesley Hyatt in 1868. This seminal invention led to the development of more sophisticated machines in the 20th century, allowing for increased production capabilities. By the 1960s and 1970s, injection molding had transformed into a highly automated process, with advancements in materials like Nylon and other thermoplastics significantly broadening its applications. The evolution of computer-aided design (CAD) and computer-aided manufacturing (CAM) further revolutionized the industry, enabling more complex shapes to be manufactured with precision.
Key Terminology in Injection Molding
To understand injection molding, several key terms are pivotal:
- Mold: The hollow form used to create the shape of the product.
- Clamping Force: The pressure required to keep the mold closed during the injection process.
- Cycle Time: The total time required to complete one injection molding cycle, including injection, cooling, and ejection.
- Thermoplastics: Plastics that can be melted and remolded multiple times.
- Thermosetting Plastics: Plastics that solidify into a permanent shape after being heated.
How Injection Molding Works
Injection Molding Process Overview
The injection molding process can be divided into several critical stages:
- Clamping: The mold is closed and clamped to withstand the injected material’s pressure.
- Injection: The molten material is injected into the mold cavity under high pressure.
- Cooling: The material is allowed to cool and solidify, taking the shape of the mold.
- Ejection: Once cooled, the mold opens and the finished part is ejected.
Materials Used in Injection Molding
Various materials can be used in injection molding, each offering distinct properties suitable for different applications. Common materials include:
- Polypropylene (PP): Lightweight, resistant to moisture and chemicals, ideal for packaging.
- Polyethylene (PE): Offers good impact resistance and flexibility; often used in containers and bottles.
- Polyvinyl Chloride (PVC): Durable and versatile, suitable for plumbing and electrical applications.
- Polystyrene (PS): Rigid and brittle, commonly used for disposable cutlery and containers.
- Engineering Plastics: Such as Nylon (PA) and Acrylonitrile Butadiene Styrene (ABS), which provide strength and thermal stability for industrial applications.
Types of Injection Molding Techniques
Several techniques can be employed in injection molding, including:
- Standard Injection Molding: The most common method for creating plastic parts by injecting molten material into a mold.
- Gas-Assisted Injection Molding: An innovative technique where gas is used to create hollow parts, reducing material consumption.
- Multicolor or Multi-Material Molding: Allows for the creation of parts that are of different colors or materials in a single cycle.
- Insert Molding: Embeds components, such as metal inserts, within the plastic part during the molding process.
- Overmolding: A method in which a second material is molded over an existing part, often used for ergonomic grips on tools.
Applications and Benefits of Injection Molding
Industries Utilizing Injection Molding
Injection molding is prevalent across various industries, providing solutions for numerous applications:
- Automotive: Used to create dashboards, bumpers, and interior components.
- Consumer Goods: Production of household items, toys, and packaging.
- Medical: Manufacturing of syringes, inhalers, and medical device housings.
- Electronics: Creating protective casings and internal components for devices.
- Aerospace: Lightweight and complex components designed for improved fuel efficiency.
Cost-Effectiveness and Efficiency
One of the main advantages of injection molding is its ability to produce large volumes of parts quickly and at a low cost per unit. The process reduces waste material significantly compared to traditional machining methods. Moreover, once a mold is created, it can be used repeatedly for the production of an extensive number of components, amortizing the initial costs over a large output. This high efficiency is particularly beneficial for industries requiring mass production, significantly impacting their production schedules and profitability.
Design Flexibility and Product Quality
Injection molding allows for intricate designs and high precision, which enables the production of complex shapes that may not be possible with other methods. The process ensures uniformity, which translates into consistent product quality across batches. Innovations such as multi-cavity molds can further enhance output while maintaining tight tolerances, thereby meeting stringent quality control standards in industries like electronics and healthcare.
Common Challenges in Injection Molding
Identifying Common Injection Molding Defects
Despite its advantages, injection molding can present several challenges, including:
- Warpage: This defect occurs when parts are unevenly cooled, leading to distortion after ejection.
- Short Shots: Failure to fill the mold completely, often caused by insufficient material or improper temperature.
- Bubbles or Voids: Air trap created within the part due to inadequate venting or trapped gas during injection.
- Flash: Excess material that seeps out between mold halves during the injection process, leading to rough edges on finished parts.
Solutions for Reducing Defects
Addressing defects in injection molding often requires a mix of stringent process controls and meticulous mold design. Solutions include:
- Optimizing mold temperatures and cooling times to minimize warpage.
- Ensuring proper material flow and venting in the mold to prevent short shots and bubble formation.
- Implementing real-time monitoring systems to track the injection process and identify deviations promptly.
Adapting Processes for Optimal Results
Continuous improvement methodologies, such as Six Sigma and Lean Manufacturing, can help streamline injection molding processes. Training personnel on best practices, conducting regular machine maintenance, and investing in updated technology are paramount to enhancing overall efficiency and reducing defects. Prototyping techniques, including 3D printing, can also aid in perfecting designs before the final production occurs.
The Future of Injection Molding
Technological Innovations in Injection Molding
As the demand for customization and faster production times rises, the injection molding industry is witnessing significant technological innovations. Innovations such as:
- Industry 4.0: The integration of IoT (Internet of Things) into manufacturing processes for real-time data collection and analysis.
- Advanced Materials: Development of new materials, including biodegradable plastics and advanced composites, expands application possibilities.
- Automation & Robotics: The use of sophisticated robots enhances efficiency and reduces human error in the molding process.
Environmental Considerations and Sustainability
With global attention on sustainable manufacturing, the injection molding industry is adapting by integrating more eco-friendly practices. This transition includes:
- Adopting recyclable materials in the injection molding process.
- Implementing energy-efficient molding machines to lessen carbon footprints.
- Enhancing recycling opportunities by improving designs for easier disassembly and recycling of components.
Trends Shaping the Industry
The landscape of injection molding is evolving, shaped by trends such as:
- The increasing popularity of electric injection molding machines for reduced energy consumption.
- Customization of products as consumers demand personalized solutions in various sectors.
- Collaboration across supply chains for enhanced material sourcing and distribution.