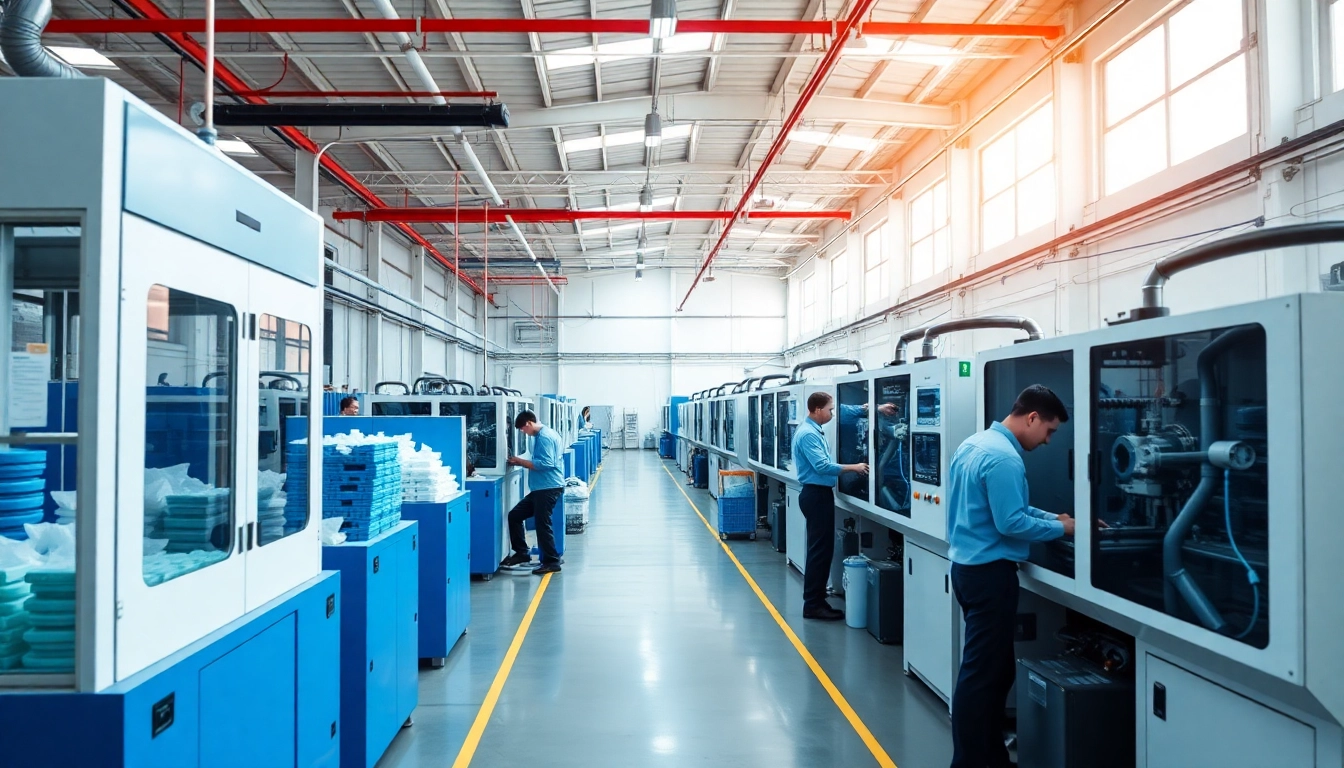
Understanding the Manufacture of Plastic Parts
Introduction to Plastic Manufacturing
The manufacture of plastic parts is an essential aspect of modern industrial production. Plastics are ubiquitous in everyday life, featured in products ranging from consumer goods to critical components in the automotive and aerospace industries. This section will illuminate the fundamental concepts of plastic manufacturing and its significance in today’s economy.
Plastic manufacturing involves a variety of processes to transform raw materials into finished products. These processes allow for versatility in fabrication, enabling manufacturers to produce complex shapes and designs efficiently. Understanding the types of plastics and their properties is crucial for selecting appropriate manufacturing methods.
Importance of Quality in Plastic Parts
Quality assurance in plastic manufacturing is paramount. Defects in plastic parts can lead to product failures, safety issues, and costly recalls. High-quality plastic parts ensure functionality, aesthetic appeal, and longevity. Significant parameters to evaluate quality include:
- Dimensional accuracy: Ensures parts fit as intended.
- Material consistency: Maintains performance across batches.
- Surface finish: Influences aesthetic and functional aspects.
- Mechanical properties: Includes strength, flexibility, and durability.
Implementing robust quality controls throughout the manufacturing process can prevent these issues. Techniques such as Six Sigma and Total Quality Management (TQM) are often employed to promote continuous improvement and minimize defects.
Common Materials Used
Plastic manufacturing utilizes a variety of polymers, each suited for specific applications. Some of the most common materials include:
- Polypropylene (PP): Known for its chemical resistance and versatility.
- Polyethylene (PE): Widely used due to its lightweight and durability.
- Polyvinyl Chloride (PVC): Common in construction and plumbing.
- Acrylonitrile Butadiene Styrene (ABS): Valued for its strength and impact resistance.
- Polycarbonate (PC): Offers high clarity and impact resistance, often used in safety applications.
Selecting the appropriate material is crucial for meeting product specifications and intended applications. Factors such as temperature tolerance, chemical exposure, and mechanical properties must be considered during the selection process.
Key Manufacturing Processes in Plastic Production
Injection Molding: The Backbone of Production
Injection molding is the most widely used process in plastic manufacturing, favored for its ability to produce high volumes of parts with exceptional precision. The process involves:
- Heating plastic pellets until melted.
- Injecting the molten plastic into a mold under high pressure.
- Cooling the mold to allow the plastic to solidify.
- Releasing the finished part from the mold.
Injection molding offers several advantages:
- High production rates: Ideal for mass manufacturing.
- Complex geometries: Capable of producing intricate designs.
- Minimal waste: Excess material can be reused in future batches.
However, the initial costs for mold creation can be significant, which necessitates a sufficient production volume to justify the investment. Proper design and mold material selection can mitigate some of these costs.
Alternative Techniques: Blow Molding and Extrusion
While injection molding holds a dominant position in plastic manufacturing, other techniques play pivotal roles as well:
- Blow Molding: Primarily used for hollow objects such as bottles. The process involves inflating a molten plastic tube (parison) within a mold to form the final shape.
- Extrusion: Suitable for producing long, continuous shapes like pipes and sheets. In extrusion, plastic is melted and forced through a die to create a specific cross-sectional profile.
These methods are employed based on the product’s design requirements and performance expectations. Choosing the right manufacturing technique can greatly enhance efficiency and reduce costs.
Comparative Analysis of Manufacturing Methods
When deciding on a manufacturing method, it is essential to weigh the pros and cons of each technique:
Process | Advantages | Limitations |
---|---|---|
Injection Molding | High volume, precision, minimal waste | High initial costs, longer setup time |
Blow Molding | Ideal for hollow items, quick cycle times | Limited to hollow shapes, less flexibility |
Extrusion | Continuous production, low waste | Less control over shape complexity |
This analysis aids manufacturers in making informed decisions about the most appropriate processes based on their product specifications and production goals.
Choosing the Right Process for Your Project
Factors Influencing Process Selection
Several key factors should be considered when selecting a manufacturing process for plastic parts:
- Volume of Production: Higher demands typically favor injection molding due to its efficiency.
- Complexity of Design: More intricate designs may necessitate injection molding to achieve the desired precision.
- Material Compatibility: Some processes are better suited for specific materials.
- Cost Constraints: Budget limitations can significantly influence the choice of manufacturing method.
A comprehensive evaluation of these factors ensures the chosen process aligns with the project’s overall goals and specifications.
Minimum Order Quantities and Customization
Understanding minimum order quantities (MOQs) is critical for companies planning to manufacture plastic parts. MOQs can vary significantly based on the selected manufacturing process:
- Injection Molding: Typically requires higher MOQs due to initial mold costs.
- CNC Machining: Can accommodate lower MOQs, ideal for prototypes and small runs.
- 3D Printing: Excellent for rapid prototyping with no MOQ restrictions.
Customizing plastic parts to meet client specifications often necessitates close collaboration with the manufacturer to ensure that design adjustments do not compromise production efficiency or affordability.
Cost Considerations and Budgeting
Understanding the cost factors associated with different manufacturing processes is vital for effective budgeting:
- Material Costs: The type of plastic affects overall costs.
- Setup Costs: Injection molding has significant initial mold costs, while other methods often have lower startup expenses.
- Production Efficiency: Higher efficiency offsets costs through reduced labor and waste.
- Post-Processing Costs: Additional treatments may be needed based on design requirements.
Cost-effective planning can often lead to enhancements in design and performance without exceeding budget limits.
Innovations in Plastic Manufacturing Technology
Automation in the Manufacturing Process
The integration of automation technology is transforming plastic manufacturing. Automated systems improve efficiency, consistency, and product quality while reducing labor costs. Key innovations include:
- Robotic Automation: Robots can manage repetitive tasks, minimizing human error.
- Smart Manufacturing: IoT devices provide real-time monitoring and analytics for increasingly efficient operations.
- Advanced Robotics: Capable of handling intricate parts and providing quality assurance at high speeds.
These advancements lead to reduced lead times and enhanced flexibility in manufacturing operations, enabling companies to adapt to changing market demands swiftly.
Sustainable Practices in Plastic Production
As environmental concerns grow, the adoption of sustainable practices in plastic manufacturing is becoming increasingly important. Companies are implementing various strategies, including:
- Recycling: Many manufacturers are integrating recycled plastics back into the production process.
- Bioplastics: Using renewably sourced materials to produce biodegradable alternatives.
- Energy Efficiency: Implementing energy-efficient machinery and practices to minimize carbon footprints.
These practices not only meet consumer demand for sustainability but often lead to cost savings through reduced material consumption and waste.
Future Trends in Plastic Manufacturing
As technology evolves, the landscape of plastic manufacturing is expected to change significantly. Emerging trends include:
- 3D Printing: Rapid prototyping and low-cost production are likely to broaden the appeal of 3D printing in creating complex geometries.
- Biodegradable Plastics: Innovations in material science, developing plastics that break down naturally.
- Advanced Materials: Development of composites with enhanced properties for specialized applications.
Staying ahead of these trends is crucial for manufacturers to remain competitive in a rapidly evolving market.
Conclusion and Next Steps for Manufacturers
Evaluating Your Manufacturing Needs
The first step in improving your approach to the manufacture of plastic parts is a thorough evaluation of your current needs. Define specific requirements based on:
- Product specifications
- Target market demands
- Budget constraints
- Volume of production needed
This analysis will allow you to align your manufacturing capabilities with market expectations effectively.
Finding the Right Manufacturing Partner
Choosing the right manufacturing partner is critical. Consider aspects such as:
- Experience and Expertise: Ensure they have a track record in your industry.
- Technology and Processes: Verify they utilize advanced manufacturing techniques and equipment.
- Quality Assurance: Look for certifications and quality control measures in place.
A strong partnership can significantly influence your production efficiency and product quality.
Continuous Improvement in Plastic Processes
Continuous improvement is an essential aspect of manufacturing success. Regularly assess processes, gather feedback, and implement improvements to maintain competitiveness. Strategies include:
- Adopting lean manufacturing principles to eliminate waste.
- Implementing regular training programs for staff to enhance skills.
- Utilizing customer feedback to drive product innovation.
Through a committed approach to improvement, manufacturers can enhance efficiency, reduce costs, and deliver higher-quality products to their customers.