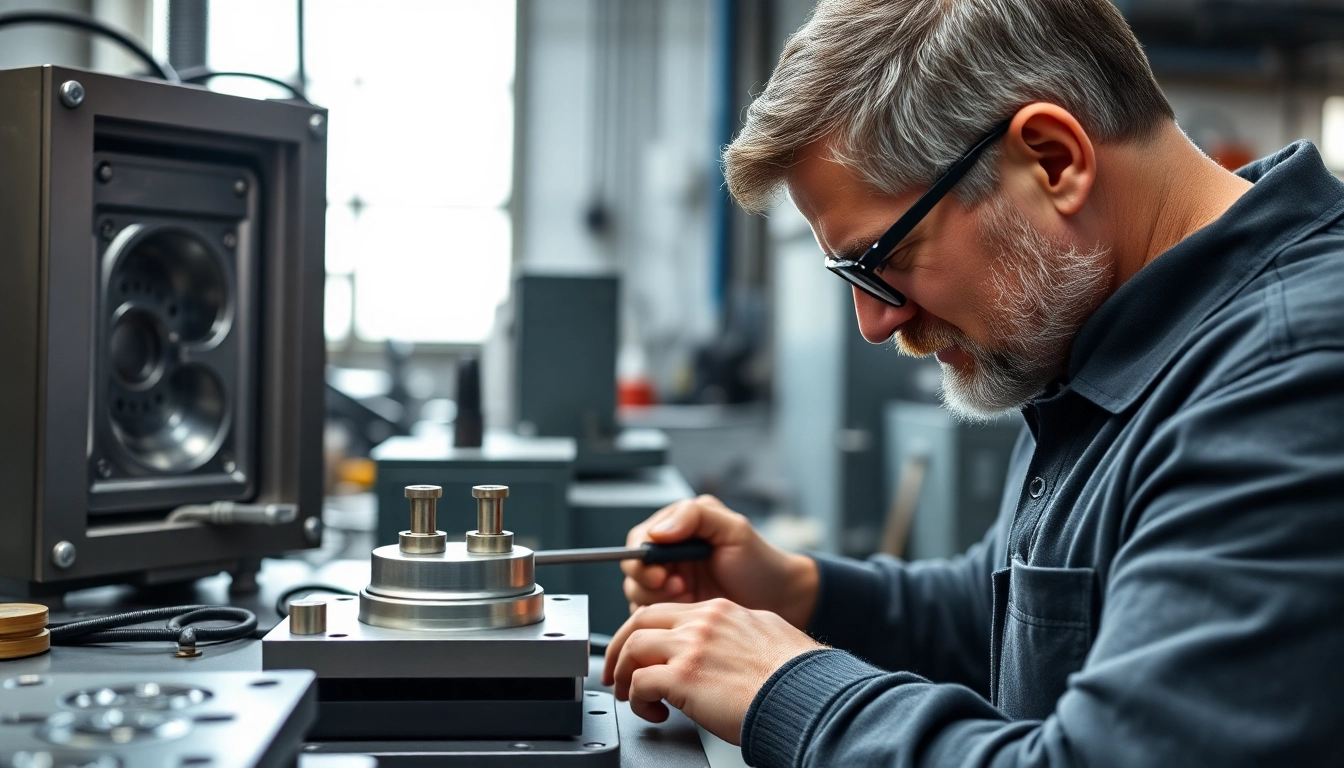
Understanding Plastic Injection Molding
Plastic injection molding is a manufacturing process that allows for the production of parts by injecting molten plastic into a mold. This method is widely adopted due to its efficiency, flexibility in design, and ability to produce high volumes of consistent parts. Understanding the fundamentals of plastic injection molding is crucial for anyone looking to work with mold makers for injection molding, as they play a pivotal role in ensuring the quality and functionality of the final products.
What is Injection Molding?
Injection molding involves a series of steps: the plastic is first melted and then injected at high pressure into a mold cavity. Once the material cools and solidifies, the mold is opened, and the newly formed part is ejected. This process can be adapted to a variety of materials, including thermoplastics, thermosets, and elastomers, making it versatile for different manufacturing needs.
The Importance of Quality Molds
The significance of high-quality molds cannot be overstated—they are the backbone of successful injection molding operations. Quality molds ensure precision in part production, reduce waste, and minimize costs over time. A well-designed mold will accommodate not only the intended design but also the materials and production techniques. Moreover, molds that are intricately designed can even offer functionalities that contribute to more efficient manufacturing processes.
Mold Maker for Injection Molding: A Key Role
The role of a mold maker is essential in the injection molding industry. These professionals are responsible for creating the molds that define the shapes and sizes of the final products. Their expertise includes understanding the nuances of various plastics, mold design, machining processes, and the ability to troubleshoot issues during the mold-making process. As a result, a skilled mold maker can greatly enhance the quality of injection molded parts.
How to Choose a Mold Maker for Injection Molding
Factors to Consider When Selecting a Mold Maker
When it comes to choosing a mold maker for injection molding, several factors should guide your decision:
- Experience: Look for mold makers with a proven track record in the industry, specifically in your area of application.
- Technology: Ensure that the company utilizes modern technology and techniques to produce their molds, including CNC machining and 3D printing.
- Material Expertise: Choose a mold maker familiar with the materials you plan to use, as different plastics require different mold designs.
- Communication: Opt for a mold maker who maintains open lines of communication throughout the process to ensure your requirements are being met.
- Timeline: Understanding their production timeline and ability to meet your deadlines is crucial for successful project management.
Evaluating Experience and Expertise
Experience in mold making is directly correlated with the quality of the final product. Evaluate potential mold makers by looking at their portfolio to see past work, especially projects similar to yours. Ask about their qualifications, backgrounds, and whether they have specialized training or certifications in injection mold design and manufacturing. Check client references to gauge their reputation and reliability in delivering projects on time and within budget.
Cost Considerations for Mold Making Services
Understanding the cost implications of mold making can be tricky. Mold costs can range from a few thousand to tens of thousands of dollars, depending on complexity, material, and production volume. It’s essential to weigh the upfront investment against long-term savings. While cheaper options may be tempting, consider the potential for increased rework, defects, and lower longevity of molds. Request detailed quotes from several mold makers and compare their offerings on more than just price, taking quality into account.
Common Types of Injection Molds
Single-Cavity vs. Multi-Cavity Molds
Molds can be categorized based on their complexity. Single-cavity molds produce one part per cycle, making them ideal for low-volume production runs. On the other hand, multi-cavity molds can produce several parts simultaneously, significantly increasing production efficiency for high-volume needs. Selecting between these types depends on the production volume, part design, and budget considerations.
Hot Runner vs. Cold Runner Systems
Injection molds can also feature hot runner or cold runner systems. In hot runner systems, the plastic is kept molten in the runner channels, allowing quicker cycle times and less waste material. Conversely, cold runner systems cool the plastic in the channels, which can lead to larger amounts of scrap. Each system has its benefits and drawbacks, and the choice often depends on the specific project requirements and production goals.
Specialized Molds for Unique Applications
Specialized molds are designed to cater to unique applications or specific industries. For instance, multi-shot molds allow for the injection of multiple materials in one cycle, creating complex parts with different properties. Additionally, molds for overmolding combine two materials to provide enhanced grip or durability. Understanding the application specifics can help mold makers create tailored solutions that meet exact functional requirements.
Best Practices in Mold Making
Materials Used in Mold Construction
The choice of materials used in mold construction can greatly influence the final quality of the injected parts. Common materials include steel and aluminum. Steel molds, while more expensive, are durable and suitable for high-volume production runs, whereas aluminum molds provide cost-effectiveness and are often used for prototyping or lower-volume applications. Selecting the right material depends on the production environment, expected lifecycle, and part requirements.
Maintenance Tips for Longevity
Regular maintenance of injection molds is essential for longevity and consistent performance. Some best practices include:
- Regular cleaning to remove debris and residue from the mold cavity.
- Routine inspections to check for wear and tear, mitigating potential issues before they escalate.
- Proper lubrication of moving parts to reduce friction and prevent breakage.
- Following a prescribed maintenance schedule based on usage to ensure optimal performance over time.
Innovations and Technology in Mold Making
Advancements in technology continue to reshape mold making. For instance, 3D printing technology is being deployed for rapid prototyping and creating complex geometries that traditional methods struggle to achieve. Additionally, computer-aided design (CAD) and computer-aided manufacturing (CAM) allow for precise mold design and quicker production times. Staying informed about technological innovations can provide mold makers with a competitive edge and further enhance the quality of their products.
Case Studies: Successful Projects by Leading Mold Makers
Examples of Custom Injection Molding Solutions
Many companies have successfully implemented custom injection molding solutions that highlight the expertise of their mold makers. For example, a leading automotive manufacturer required specialized molds for complex car parts that needed to meet stringent safety and durability standards. The mold maker’s ability to innovate by using multi-cavity molds resulted in improved production times and reduced costs, demonstrating the value of skilled mold makers in achieving business objectives.
Challenges and Solutions in Mold Making
Throughout the mold-making process, challenges inevitably arise. For instance, achieving precise tolerances can be difficult, especially with intricate designs. A common solution involves iterative prototyping and robust testing methods to ensure that molds are properly aligned and functioning as intended. Another challenge is material compatibility; mold makers must ensure the selected materials withstand the heating and cooling cycles without degrading. Addressing these challenges requires a blend of technical skill, innovative thinking, and effective communication with clients.
Client Testimonials and Success Stories
Real-world testimonials from clients can provide insight into the effectiveness of specific mold makers. One client noted that their partnership with a particular mold manufacturer led to a 20% reduction in production costs due to the precision of the molds produced. Such success stories help validate the capabilities of mold makers and offer proof of their contribution to the projects they handle. Engaging in open dialogue with previous clients can further aid in assessing a mold maker’s reliability and expertise.