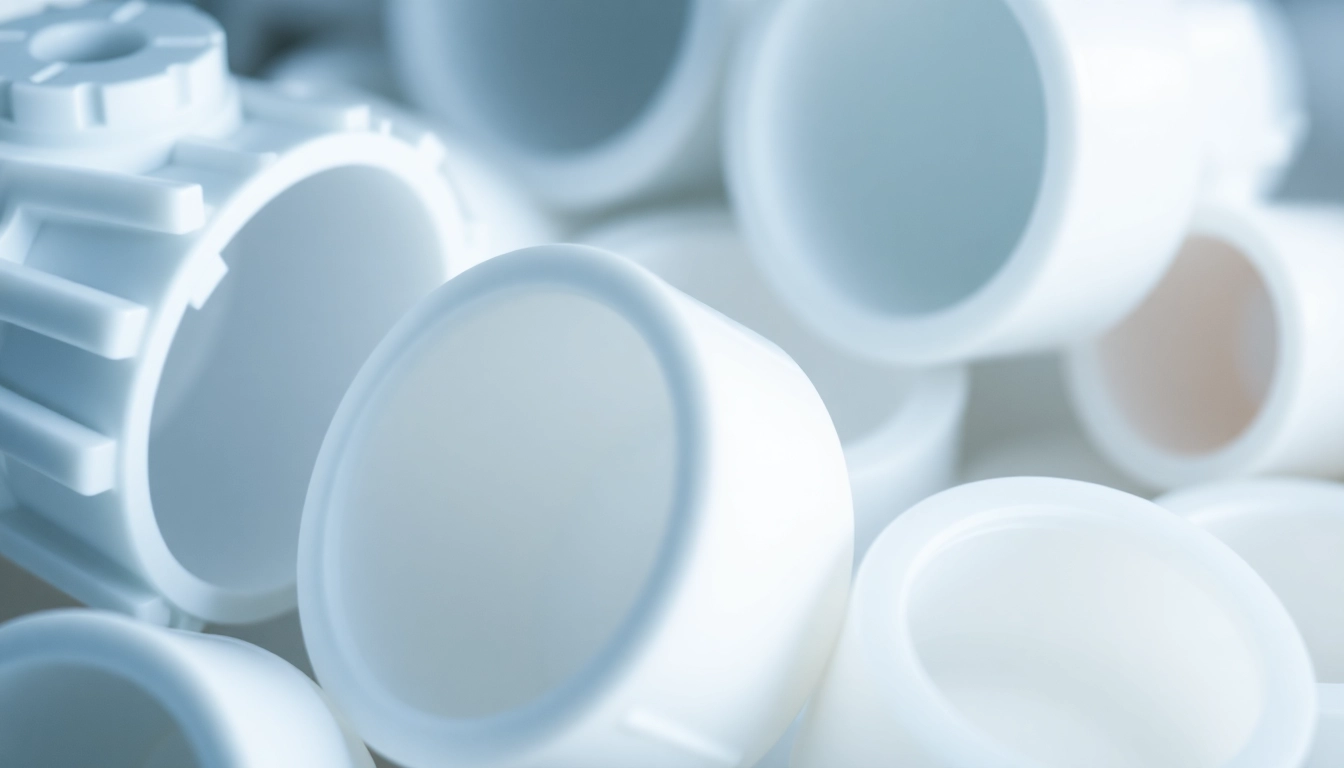
Understanding Blow Moulded Plastic Parts
Definition and Overview
Blow moulding is a specialized manufacturing process primarily used for the production of hollow plastic parts. This innovative technique involves inflating a thermoplastic tube, known as a parison, into a mould to create various shapes and sizes. The versatility of blow moulding makes it an industrial choice for crafting products that are lightweight yet robust, accommodating a wide range of applications, from containers to automotive components.
The significance of blow moulded plastic parts cannot be understated, as they play a pivotal role across numerous sectors. The process is efficient, capable of producing high volumes of parts quickly, thus reducing manufacturing time and costs while maintaining consistent quality across outputs.
Key Materials Used
The materials utilized in blow moulding are crucial to the performance and sustainability of the final product. Common materials include:
- Polyethylene (PE): Available in various densities (LDPE, HDPE, LLDPE), polyethylene is one of the most widely used polymers in blow moulding, renowned for its strength and flexibility.
- Polypropylene (PP): Known for its high chemical resistance and fatigue tolerance, polypropylene is suited for both high-temperature applications and those exposed to moisture.
- Polyethylene Terephthalate (PET): PET is primarily utilized for beverage bottles due to its excellent clarity and moisture barrier properties.
- Polyvinyl Chloride (PVC): Often used in construction and manufacturing applications, PVC is respected for its durability and resistance to environmental effects.
Each of these materials presents specific advantages and challenges, making the selection process critical based on the intended use of the blow moulded part.
Common Applications in Industry
Blow moulding finds its way into many industries due to its adaptability and efficiency. Notable applications include:
- Packaging: A significant percentage of blow moulded products are containers and bottles for beverages, cleaning agents, and cosmetics.
- Automotive: Components such as air ducts, fuel tanks, and exterior housing parts are efficiently produced using blow moulding.
- Consumer Goods: Household items, toys, and sports equipment often leverage blow moulding for their designs.
The Blow Moulding Process Explained
Types of Blow Moulding Techniques
Understanding the various blow moulding techniques is key to appreciating their application, and they can be broadly classified into:
- Extrusion Blow Moulding (EBM): This is the most common technique where a continuous parison is extruded, and a mould forms around it to shape the final product.
- Injection Blow Moulding (IBM): This method combines injection moulding and blow moulding, where pre-formed parts are placed in a mould and inflated.
- Injection Stretch Blow Moulding (ISBM): Similar to IBM, ISBM incorporates a stretching process which provides higher clarity and strength, primarily used for making PET bottles.
Step-by-Step Guide to Blow Moulding
The blow moulding process involves several steps:
- Preparation of the Parison: A thermoplastic resin is heated to a viscous state and formed into a tubular shape.
- Molten Material Insertion: The heated parison is positioned between two halves of a mould.
- Inflation: Compressed air is introduced, inflating the parison to conform to the mould shape.
- Cooling: The mould is cooled, allowing the plastic to solidify while maintaining its shape.
- Mould Opening and Finishing: Once cooled, the mould opens, and the finished part is ejected. Any necessary trimming or finishing processes are conducted.
Factors Affecting Production Quality
Numerous factors influence the quality of blow moulded parts:
- Material Consistency: Variability in the raw material can lead to defects.
- Mould Design: An intricately designed mould that allows for smooth fluidity of the material can significantly reduce imperfections.
- Temperature Control: The temperature of the plastic at all stages must be well-monitored to prevent issues like warping or insufficient inflation.
Advantages of Blow Moulded Plastic Parts
Cost-Effectiveness in Manufacturing
One major advantage of blow moulding lies in its cost-effectiveness. This production method enables manufacturers to produce large quantities of parts rapidly, minimizing labor costs and reducing the time required for changeovers and setups. This efficiency is a core reason why industries favor blow moulding, particularly when high-volume production is needed.
Lightweight yet Durable Characteristics
Blow moulded plastic parts are celebrated for their lightweight nature, which can lead to reductions in transportation costs and energy consumption. This characteristic is especially beneficial in the automotive industry, where decreasing weight is a priority for fuel efficiency and performance. Furthermore, many blow moulded materials offer considerable environmental resistance, leading to durability in various applications.
Customization and Design Flexibility
The blow moulding process accommodates an extensive range of designs, patterns, and finishes, allowing for high degrees of customization. Designers and engineers can create complex shapes that meet specific aesthetic and functional requirements. This flexibility extends to textures, colors, and branding elements, making blow moulding an attractive option for consumer goods manufacturers.
Challenges in Blow Moulding
Common Production Issues and Solutions
While blow moulding offers various benefits, several challenges can arise during production:
- Defects in Finished Products: Issues such as uneven wall thickness or air bubbles can occur. Regular maintenance of moulds and precise control of processing parameters can mitigate such challenges.
- Mould Design Limitations: Inflexible designs may hinder product variations. Collaborating with experienced mould designers can ensure adaptability and versatility in production.
Material Limitations and Alternatives
Despite the widespread use of specific materials, limitations exist based on the intended application. For instance, while polyethylene is ubiquitous for its low cost, it may not provide the mechanical strength required for structural components. In such cases, alternatives like polypropylene or engineering plastics may represent more suitable choices depending on the project requirements.
Environmental Considerations
The production and recycling of blow moulded parts entail environmental implications. The industry is witnessing a shift towards sustainable practices, such as utilizing biodegradable materials and improving recyclability. Innovations in recycling technologies are also being explored, allowing companies to reclaim resources from used products, thus minimizing waste.
Future Trends in Blow Moulding Technology
Innovations in Sustainable Materials
The focus on sustainability is not just a trend but an evolving necessity within the blow moulding industry. The introduction of bio-based and recycled materials is gaining momentum, aligning production with environmental standards while providing manufacturers with alternatives that do not compromise product quality.
Advancements in Manufacturing Technologies
The blow moulding process is continuously evolving through technological advancements. Automation and smart manufacturing techniques are becoming prevalent, enhancing accuracy in moulding, reducing machine downtime, and optimizing production efficiencies. The incorporation of IoT devices in machinery allows for real-time monitoring, contributing to improved quality control and reduced waste.
Market Outlook for Blow Moulded Products
Market trends indicate a growing demand for blow moulded products due to their adaptability and cost-effectiveness across various applications. As industries seek lighter, more efficient materials to meet evolving consumer preferences and regulatory requirements, the blow moulding sector is poised for steady growth. Moreover, the integration of sustainable practices within the production process will likely differentiate leading manufacturers in the competitive landscape.