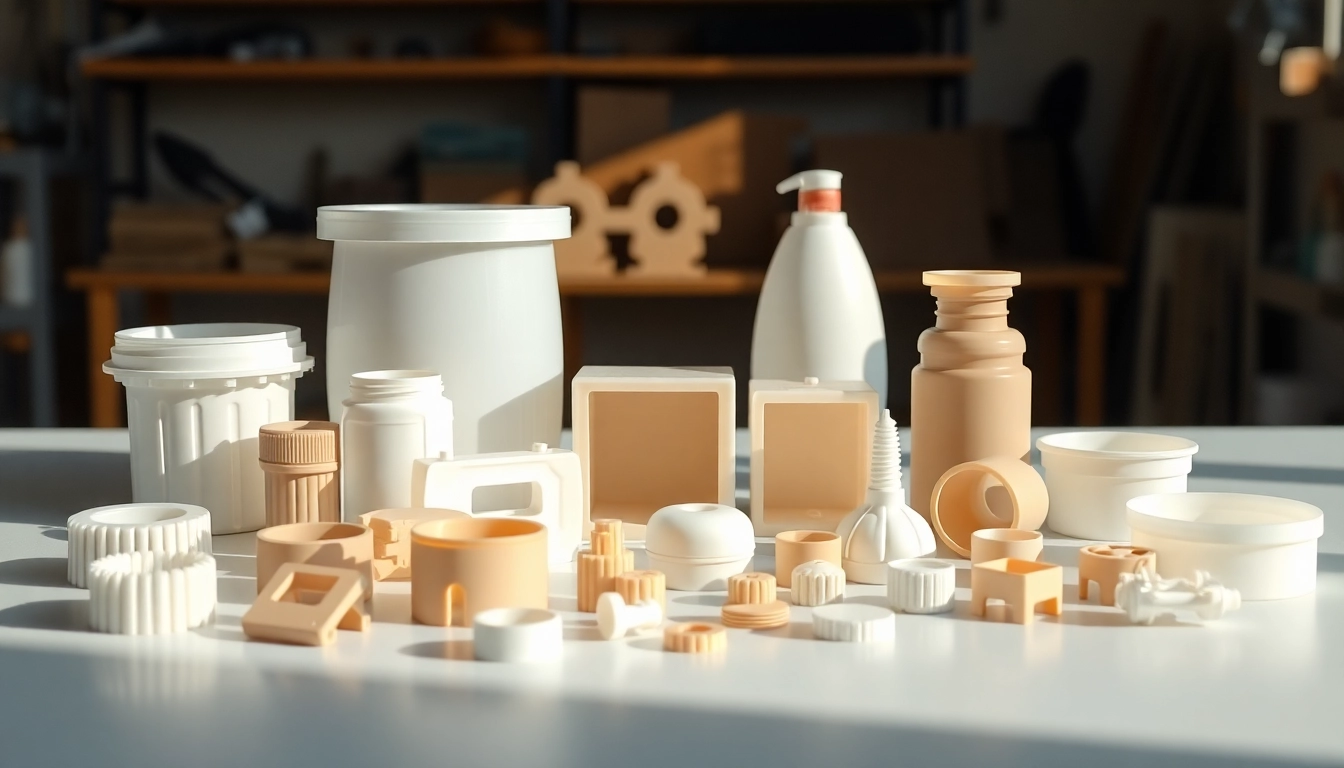
Understanding Injection Molded Parts
Injection molded parts are predominant in modern manufacturing, shaping the way products are designed and produced across various industries. From intricate components in electronics to consumer products found in every home, the significance of injection molded parts cannot be understated. This guide delves into the intricacies of injection molding, examining the process, the components involved, applications, benefits, challenges, and future trends in the production of these vital parts.
What are Injection Molded Parts?
Injection molded parts are components created through the injection molding process, where molten plastic is injected into a mold cavity under pressure. The result is a solidified part that closely follows the mold’s shape and intricacies. This method allows for high-speed production of complex geometries with a minimal margin for error, which is vital for maintaining quality in mass production.
The Injection Molding Process Explained
The injection molding process consists of several stages, each crucial for ensuring the final part meets quality standards:
- Material Preparation: The selected plastic pellets are fed into a hopper and then conveyed to the injection unit.
- Melting: The pellets are heated until they melt and are transformed into a viscous fluid suitable for injection.
- Injection: The molten plastic is injected into the mold at high pressure, filling the cavity completely.
- Cooling: The injected material cools and solidifies inside the mold, taking the shape of the design.
- Ejection: Once cooled, the mold opens, and ejector pins push the molded part out for inspection and packaging.
This process allows manufacturers to achieve high production speeds, making it ideal for producing large quantities of identical parts efficiently.
Common Applications of Injection Molded Parts
Injection molded parts find applications across various sectors. Some prominent examples include:
- Consumer Products: Items like plastic containers, toys, and household tools.
- Automotive Components: Dials, dashboards, and interior trim parts are often made using injection molding due to the precision required.
- Medical Devices: Parts for syringes, inhalers, and other medical equipment benefit from the consistent quality offered by this manufacturing process.
- Electronics: Enclosures and housings for devices such as smartphones, computers, and appliances.
Key Components of Injection Molding
Essential Parts of an Injection Mold
Understanding the anatomy of an injection mold is crucial for grasping how injection molded parts are created. Key components include:
- Mold Base: The structure that supports the mold and ensures alignment.
- Core and Cavity: The core forms the internal features of the part, while the cavity gives the exterior shape.
- Runner System: Channels that guide the molten plastic into the mold cavities.
- Ejector System: Mechanisms that remove the finished part from the mold.
Types of Materials Used for Injection Molded Parts
The choice of materials is fundamental in injection molding. Various plastics can be used, allowing for tailored properties in final products:
- Thermoplastics: Commonly used due to their ability to be reheated and reshaped. Examples include ABS, polycarbonate, and polystyrene.
- Thermosets: These materials undergo a chemical change when heated, creating strong and durable parts. Examples include epoxy resins and silicone.
- Elastomers: These are rubber-like materials often used in applications requiring flexibility and high impact resistance.
Design Considerations for Effective Molding
Optimizing the design of injection molded parts is crucial for ensuring manufacturability and effectiveness. Important considerations include:
- Draft Angles: Proper draft angles facilitate easier ejection from molds without damaging parts.
- Wall Thickness: Uniform wall thickness minimizes warping and ensures consistent cooling and strength.
- Radii and Fillets: Implementing rounded edges can help reduce stress concentrations and enhance flow during molding.
Benefits of Using Injection Molded Parts
Cost Efficiency and Production Speed
One of the primary advantages of injection molding is the economic benefit derived from high-volume production. The initial investment in molds may be substantial, but the per-unit cost decreases with higher quantities. As a result, many large manufacturers opt for injection molding when producing thousands of parts, significantly lowering costs.
Precision and Quality Control
Injection molding provides a high level of accuracy in producing parts. The stability of the process allows for tight tolerances to be achieved consistently, which is vital for applications in sectors like automotive and medical devices. The ability to monitor and control the molding parameters also enhances quality assurance throughout production runs.
Versatility in Design and Functionality
The versatility of injection molding allows manufacturers to create complex shapes that would be challenging with other methods. This flexibility enables innovations in product design, such as incorporating features directly into products rather than additional assembly processes later.
Challenges in Injection Molding
Common Issues Encountered in Production
While injection molding presents numerous advantages, it is not without challenges. Common issues faced during production include:
- Flash: An undesirable surplus of material seeping out of the mold due to insufficient tightening.
- Short Shots: Occurs when insufficient material fills the mold cavity, leading to incomplete parts.
- Warpage: This can happen due to uneven cooling rates or improper part design.
How to Troubleshoot Molding Problems
Troubleshooting mold issues requires a systematic approach. Key strategies include:
- Adjust Mold Temperature: Ensuring proper heating and cooling cycles can help solve warping and short shots.
- Optimize Injection Speed: Tuning the speed can reduce the occurrence of defects like flash and short shots.
- Monitor Material Quality: Ensuring that the material used meets specifications can prevent many quality issues.
Maintaining Quality throughout the Injection Molding Process
Maintaining quality in injection molding requires continual oversight at every stage. Regular inspections, in-process quality checks, and embracing continuous improvement processes can contribute significantly to maintaining consistent quality.
Future Trends in Injection Molded Parts
Advancements in Technology and Materials
The injection molding industry is increasingly leveraging new technologies, enhancing both efficiency and adaptability. Advancements such as:
- 3D Printing of Molds: Using additive manufacturing to create molds can reduce lead times for prototypes.
- Smart Injection Molding: Incorporating IoT-enabled equipment allows for real-time monitoring and adjustments to the molding process.
The Rise of Sustainable Molding Solutions
Sustainability is a growing focus within the industry. Innovations such as biodegradable plastics and recycling of scrap plastic are gaining traction. Additionally, processes are being developed to minimize waste and energy consumption, aligning manufacturing with environmental goals.
Emerging Markets for Injection Molded Parts
As global markets evolve, new opportunities are arising for injection molded parts. Markets such as electric vehicles, renewable energy solutions, and medical technology are expanding the demand for sophisticated injection-molded components, suggesting a robust future for the industry.