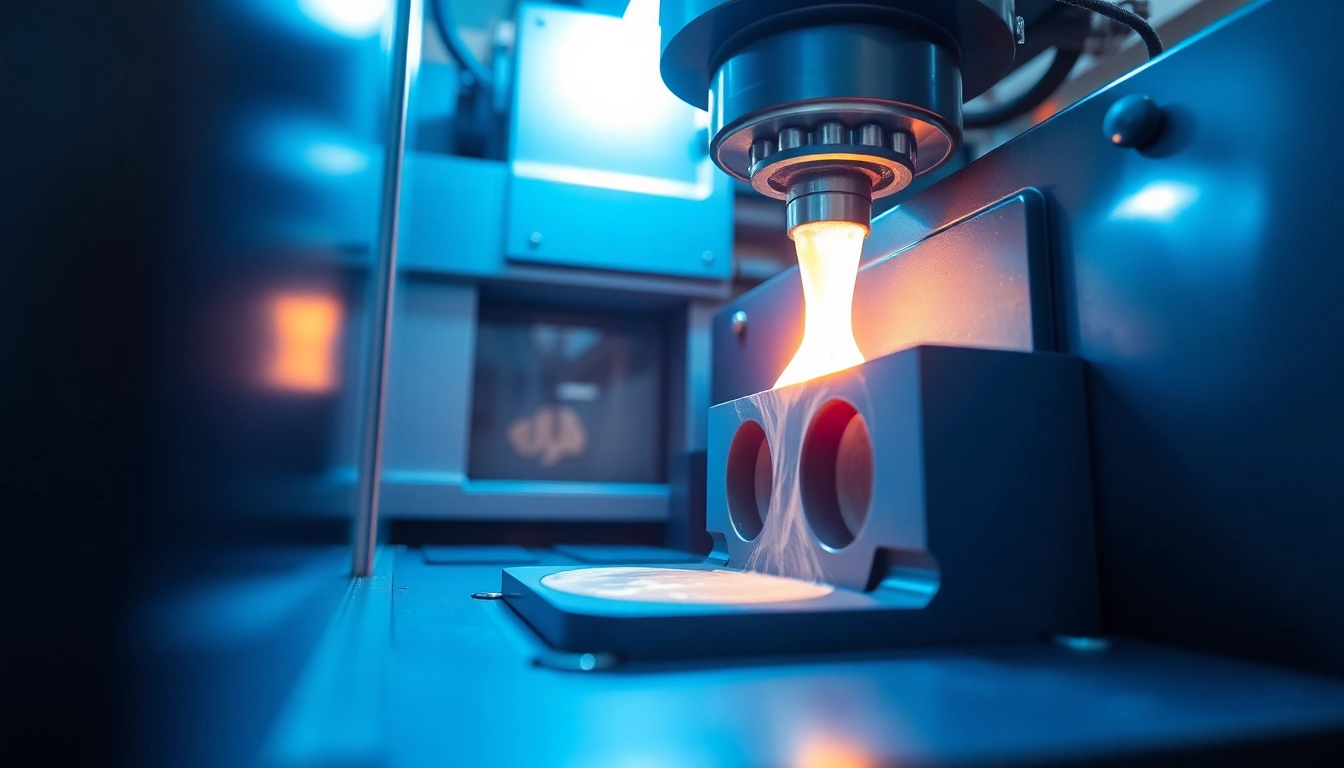
Understanding Injection Molding
Injection molding is a highly efficient manufacturing process that has fundamentally transformed the production of plastic parts across various industries. It involves the injection of molten material into a precisely shaped mold, allowing for the mass production of intricate components with high levels of accuracy and repeatability. As industries continue to innovate and expand, understanding the nuances of injection molding becomes increasingly essential for manufacturers seeking to leverage this technique effectively.
What is Injection Molding?
At its core, injection molding is a process designed for mass-producing items with complex geometries and tight tolerances. The process begins with heating plastic granules until they melt into a viscous form. This molten plastic is then injected into a mold cavity under high pressure. Once the material cools and solidifies, the mold is opened, and the finished product is ejected. This methodology can be applied to various thermoplastics, thermosetting polymers, and even some metals, making it one of the most versatile manufacturing processes available.
Key Benefits of Injection Molding
Injection molding offers several significant advantages that contribute to its popularity in manufacturing. These include:
- Precision: The process allows for extremely tight tolerances, ensuring that parts fit together correctly in assembly.
- Efficiency: Once the mold is created, the cycle time for production is quick, often ranging from a few seconds to several minutes per part.
- Material Versatility: A wide range of materials can be used in injection molding, including various plastics and metals.
- Cost-Effectiveness: For large production runs, injection molding is one of the most economical manufacturing methods, particularly due to its low per-unit cost.
- Design Flexibility: Injection molding supports complex designs that are often impossible to produce through other manufacturing methods.
Main Applications of Injection Molding
Injection molding is employed in several industries, including:
- Automotive: Used for producing interior and exterior components such as dashboards and bumpers.
- Consumer Goods: Common in items like containers, toys, and electronics enclosures.
- Medical: Essential for manufacturing devices like syringes and polymeric housings for medical instruments.
- Aerospace: Utilized for creating lightweight and durable plastic parts that meet strict safety standards.
The Injection Molding Process Explained
To fully appreciate injection molding, one must understand the steps involved in the process, from material selection to the final ejection of molded parts.
Stages of Injection Molding
The injection molding process can be broken down into several distinct stages:
- Clamping: The mold is securely held in place by a clamping unit to resist the pressure generated during injection.
- Injection: Molten plastic is injected into the mold cavity.
- Cooling: The material is allowed to cool, solidifying it into the desired shape.
- Ejection: The mold opens to release the finished part, often assisted by ejector pins or plates.
This cycle typically lasts between 30 to 120 seconds, depending on the part’s size and complexity.
Materials Used in Injection Molding
A diverse range of materials can be employed in injection molding, each offering unique properties useful for specific applications. The most commonly used materials include:
- Thermoplastics: Such as polyethylene, polypropylene, and polystyrene, known for their ability to be melted and remolded.
- Thermosetting Plastics: Plastics that set into an irreversible shape when heated, such as epoxy and phenolic resins.
- Elastomers: Flexible, rubber-like materials that can be injected, suitable for seals and gaskets.
- Metal Alloys: Some processes allow for the injection of molten metals, particularly in specialized applications.
Common Types of Injection Molding Equipment
The efficiency and outcome of the injection molding process heavily depend on the type of equipment used. Key equipment includes:
- Injection Molding Machines: The heart of the operation, combining injection and clamping units.
- Molds: Custom-designed components that define the shape of the final product.
- Auxiliary Equipment: Includes temperature controllers, drying systems, and robotic systems for automation.
Design Considerations for Injection Molding
Designing parts for injection molding requires careful consideration to ensure successful results. Proper design can significantly improve the efficiency of the production process and the quality of the final product.
Creating Effective Molds for Injection Molding
Creating effective molds is crucial to the injection molding process. Molds should be designed with specific features in mind, such as:
- Draft Angles: Slight angles allow for easier ejection of parts.
- Wall Thickness: Consistent wall thickness helps prevent defects like warping and ensures even cooling.
- Fillets and Rounding: Helps to reduce stress concentrations and enhance the flow of the molten material.
Design Flaws to Avoid in Injection Molding
Common design flaws can lead to production issues, such as:
- Insufficient Draft: Leads to difficulty in ejecting parts and potential damage to the mold.
- Poor Venting: Can cause trapped air, leading to defects in the final part.
- Excessive Complexity: Unreasonably complex parts may complicate mold manufacturing and operation.
Innovative Designs for Enhanced Performance
Innovative designs can offer enhanced performance and manufacturing efficiency. Some approaches include:
- Topology Optimization: Reduces weight while maintaining structural integrity.
- 3D Printing of Molds: Expands design possibilities and speeds up prototyping.
- Integration of Multiple Features: Designing parts that incorporate multiple functionalities to reduce assembly needs.
Common Challenges in Injection Molding
Despite its many advantages, injection molding is not without its challenges. Manufacturers must be prepared to navigate various obstacles to maintain operational efficiency.
Addressing Quality Control Issues
Quality control is vital in injection molding. Common issues include:
- Defects: Surface imperfections, dimensional variations, and other flaws can arise during production.
- Material Variability: Inconsistent material properties can lead to performance issues.
- Machine Calibration: Regular calibration is crucial to maintain precise control over the molding process.
Understanding Defects in Injection Molding
Defects can significantly impact the quality of the final product. Some common defects include:
- Brittleness: Often a result of incorrect material choice or processing parameters.
- Flash: Excess material that escapes the mold, leading to unwanted protrusions.
- Warping: Uneven cooling or material shrinkage causes distortion in the final part.
Strategies for Reducing Waste and Increasing Efficiency
Improving efficiencies and reducing waste in injection molding can lead to significant cost savings. Effective strategies include:
- Optimizing Cycle Times: Utilize efficient per-cycle practices and regular maintenance to reduce idle times.
- Advanced Monitoring: Implement real-time monitoring of machines to identify and rectify issues quickly.
- Material Recycling: Reprocessing scrap material can minimize waste and reduce material costs.
Future Trends in Injection Molding
The injection molding industry is continually evolving, adapting to new technologies, and addressing the demand for sustainability.
Technological Advancements in Injection Molding
Innovations shaping the future of injection molding include:
- Industry 4.0 Integration: The incorporation of IoT technologies enables smarter manufacturing processes.
- Advanced Simulation Software: Enhances the ability to predict and optimize outcomes before production.
- Micro-Molding Techniques: Allows for the production of smaller, complex parts critical for markets such as electronics and medical devices.
Sustainable Practices in Injection Molding
As sustainability becomes more crucial, the injection molding industry is transitioning toward greener practices through:
- Biodegradable Materials: The development and use of eco-friendly materials that reduce environmental impact.
- Energy-Efficient Machines: Investing in machinery that decreases energy consumption during the molding process.
- Reusable Molds: Designing molds for multiple uses to minimize the need for new mold production.
The Role of Automation in Injection Molding
Automation is revolutionizing the injection molding sector, focusing on:
- Streamlined Production: Automated systems enhance cycle times and reduce labor costs.
- Increased Accuracy: Robots and automated systems can perform repetitive tasks with higher precision than human operators.
- Data Collection and Analytics: Automation facilitates data collection, allowing manufacturers to analyze processes and improve overall efficiency.