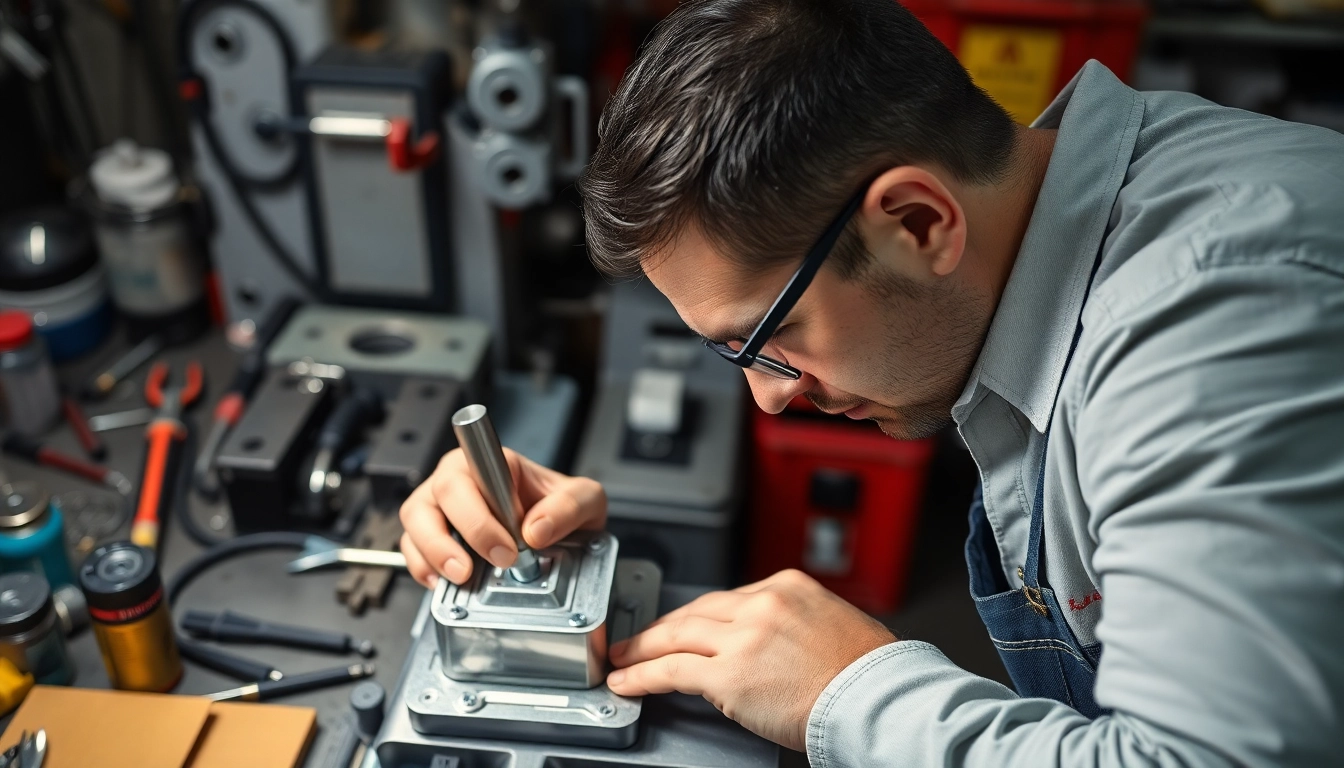
Understanding the Role of a Mold Maker for Injection Molding
The world of injection molding revolves around its key component: the mold. Within this ecosystem, the expertise of a mold maker for injection molding stands out as critical. Mold makers are the artisans behind the molds that shape everything from everyday household items to complex industrial components. Understanding their role, skills, and the types of molds they create is essential for businesses looking to succeed in manufacturing.
The Definition of a Mold Maker
A mold maker is a skilled tradesperson who designs, fabricates, and maintains molds used in the injection molding process. This role involves a blend of artistry and engineering, demanding a deep understanding of materials, machining techniques, and manufacturing processes. Mold makers work closely with designers to create precise, durable molds that can withstand the pressures of high-volume production. Their work impacts not only the aesthetic and functional qualities of the final product but also its manufacturing efficiency and cost-effectiveness.
Key Skills Required for Mold Making
The craft of mold making requires a diverse skill set that combines technical expertise with creative problem-solving. Some of the essential skills include:
- Technical Proficiency: A solid grounding in computer-aided design (CAD) software is crucial for mold makers, enabling them to create precise blueprints.
- Machining Skills: Expertise in various machining processes, including milling, turning, and electrical discharge machining (EDM), is necessary to fabricate molds accurately.
- Material Knowledge: Understanding different materials and their properties ensures that mold makers select the best options for durability and performance.
- Problem-Solving Abilities: The design and production of molds often present challenges that require innovative solutions to meet design specifications and production timelines.
- Attention to Detail: Precision is the hallmark of a successful mold maker. Small discrepancies can lead to significant issues in the mold’s performance and the quality of the final product.
Different Types of Injection Molds
Injection molds come in various types, each tailored to specific applications and manufacturing needs. The primary categories include:
- Single-Cavity Molds: These molds produce one part per cycle and are ideal for low-volume production runs.
- Multi-Cavity Molds: Designed to create multiple parts simultaneously, these molds significantly increase production efficiency and are advantageous for high-volume manufacturing.
- Family Molds: Family molds allow the production of different parts in a single cycle, optimizing efficiency and minimizing costs.
- Hot Runner Molds: These molds use a heating mechanism to keep the plastic in a molten state, reducing waste and providing greater control over the injection process.
- Cold Runner Molds: Unlike hot runner molds, these rely on cooling systems and are typically more economical for low-volume applications.
Evaluating Mold Makers: What to Look For
Choosing the right mold maker is pivotal for ensuring the success of your injection molding projects. Several factors can guide this selection process.
Experience and Technical Expertise
When evaluating potential mold makers, it’s essential to assess their experience in the industry. A seasoned mold maker will have a robust portfolio showcasing their previous work, demonstrating their ability to meet diverse manufacturing challenges. They should possess familiarity with the latest technologies and methodologies in mold making, including 3D printing and advanced machining techniques.
Quality of Past Work and Portfolio
Reviewing a prospective mold maker’s portfolio provides valuable insights into their craftsmanship and reliability. Look for evidence of precision in their work, such as the dimensional accuracy of molds and the surface finishes achieved. Additionally, inquire about the types of projects they have handled, particularly those similar to your needs, to gauge their capability effectively.
Customer Testimonials and Reviews
Customer feedback can be a telling indicator of a mold maker’s performance. Seek testimonials from past clients to understand their experiences, particularly regarding communication, adherence to timelines, and the quality of molds produced. Online reviews and ratings can also offer additional perspectives on a mold maker’s reputation in the industry.
Cost Factors Influencing Mold Maker Selection
Cost is often a significant concern when selecting a mold maker. However, understanding the various factors that influence pricing can aid in making an informed decision.
Understanding Cost Ranges for Injection Molds
The cost of injection molds can vary drastically based on complexity, size, and functionality. Simple molds may start from $3,000 while more sophisticated designs, such as multi-cavity molds or those needing intricate features, can reach $100,000 or more. Understanding these ranges can help you set realistic budgets for your projects.
Comparing Quotes from Different Mold Makers
When obtaining quotes from various mold makers, it’s essential to ensure that the comparisons are equitable. Request detailed breakdowns of costs, including material expenses, labor, and any additional services like post-production modifications or maintenance. A higher initial price may be justifiable if it reflects better craftsmanship or more durable mold materials.
Long-Term Value Over Initial Investment
While it may be tempting to choose the lowest bid, it’s crucial to consider the long-term value that a quality mold maker can provide. Investing in higher-quality molds can lead to lower defect rates, longer service life, and ultimately greater cost savings over time. Evaluate potential savings against your initial investment to make a well-rounded decision.
Best Practices for Collaborating with a Mold Maker
Building a strong working relationship with your mold maker is essential for a successful outcome. The following best practices can guide your collaboration.
Communicating Your Design Specifications
Clear and open communication is vital at every stage of mold making. Begin by providing detailed design specifications and expectations to ensure the mold maker fully understands your requirements. Utilize drawings, CAD models, and even physical prototypes if possible to convey your vision accurately.
Establishing a Clear Project Timeline
A well-defined project timeline is essential for managing expectations on both sides. Work with your mold maker to develop a schedule that includes crucial milestones such as design reviews, prototyping, and final production. Regular check-ins can help catch potential delays early and keep the project on track.
Maintaining Open Lines of Communication
Encourage ongoing dialogue throughout the entire process. Foster an environment where both parties feel comfortable discussing challenges, modifications, or ideas. This transparency can often lead to discovering better solutions and enhancements that benefit the final product.
Future Trends in Mold Making for Injection Molding
As technology and manufacturing practices evolve, the mold-making industry is witnessing significant changes. Keeping an eye on these trends can provide insight into the future landscape of injection molding.
Advancements in Mold Making Technology
Innovation in mold-making technology is rapidly changing the way molds are designed and produced. Techniques like additive manufacturing and 3D printing allow for quicker prototype development and the implementation of complex geometries that were previously unimaginable. Additionally, advancements in simulation software enable mold makers to predict potential issues early in the design process, leading to more reliable and efficient outcomes.
Shifts in Manufacturing Practices
The manufacturing sector is increasingly leaning toward automation and smart technologies. As manufacturers adopt more automated systems, mold makers are required to understand and integrate these technologies into their designs to ensure compatibility with modern production lines. This shift not only increases production efficiency but also minimizes human error.
Sustainability in Mold Making Techniques
With an increasing focus on sustainability, mold makers are beginning to adopt practices that minimize waste and reduce their environmental footprint. Utilizing recyclable materials and sustainable production methods is becoming the norm, ensuring that molds not only meet performance standards but also align with eco-friendly practices. This trend is likely to influence client choices moving forward, as companies seek partners who prioritize sustainability.