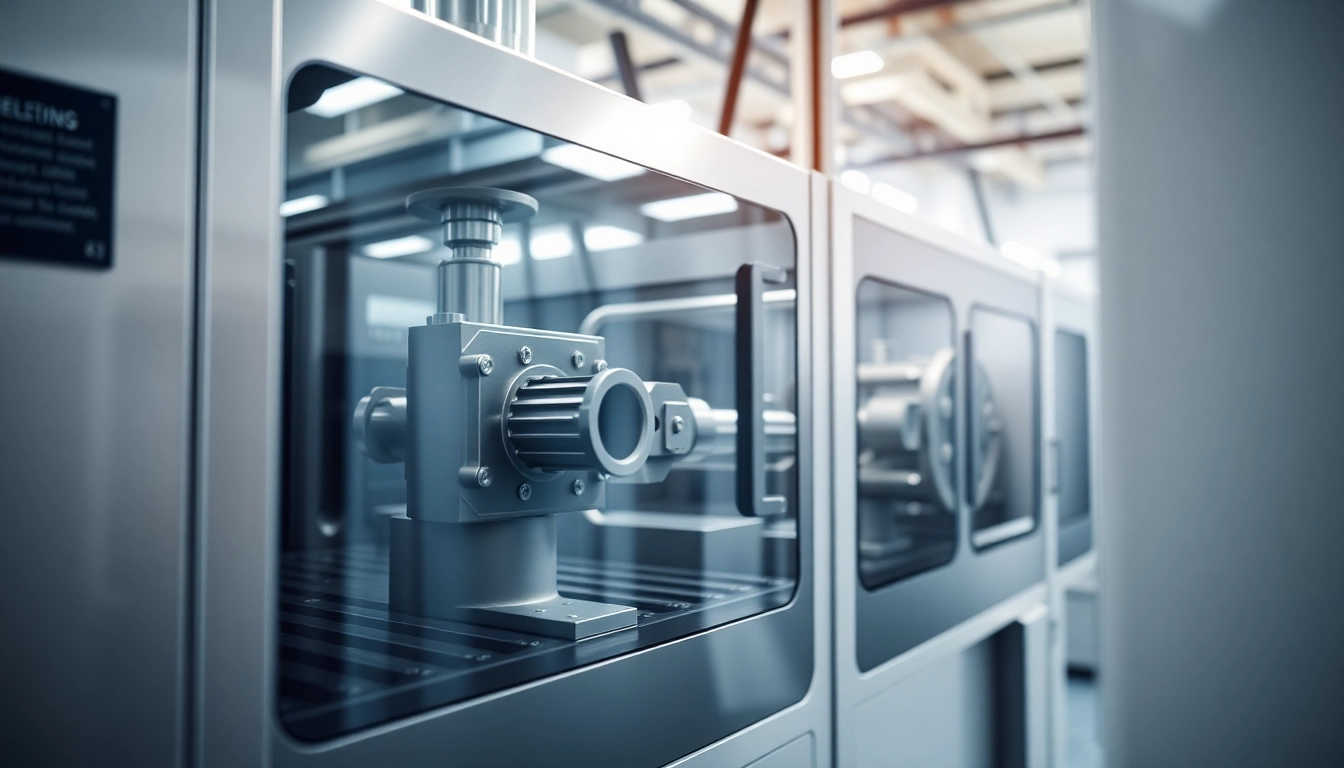
Introduction to Injection Molded Parts
Injection molded parts are integral components in countless industries, ranging from automotive and consumer electronics to healthcare and more. By employing advanced molding techniques, manufacturers create precise and complex shapes optimized for functionality and efficiency. This article delves deep into the world of injection molded parts, exploring their definition, history, benefits, the molding process, design considerations, applications, and future trends. With a comprehensive understanding, businesses can make informed decisions regarding the use of injection molded parts in their products.
What are Injection Molded Parts?
Injection molded parts are objects created through the injection molding process, where molten material is injected into a metal mold, allowed to cool, and subsequently ejected to form a solid product. The materials commonly used include various plastics, thermoplastics, thermosetting plastics, and even metals in specialized cases. This process is widely favored for its efficiency in producing large quantities of uniform parts with high precision.
History of Injection Molding
The roots of injection molding can be traced back to the early 1800s, with the invention of the first plastic, Parkesine, by Alexander Parkes. However, it wasn’t until 1872 that the first real injection molding machine was patented by John Wesley Hyatt, utilizing a simple hand-operated plunger to inject heated materials into molds. Over the years, advancements in technology, such as the introduction of thermostatic plastics in the 1920s, have significantly enhanced the capabilities and applications of injection molding, leading to its widespread adoption in manufacturing today.
Benefits of Using Injection Molded Parts
Injection molding offers numerous advantages, making it a preferred choice for many manufacturers:
- High Efficiency: The process allows for rapid production cycles, significantly reducing lead times and labor costs.
- Precision: Modern injection molding machines can achieve tight tolerances, ensuring consistent part quality.
- Material Versatility: A wide range of materials can be used, including various plastics, elastomers, and even bio-based materials.
- Complex Geometries: Injection molding enables the creation of intricate designs that would be difficult or impossible to achieve with other manufacturing methods.
- Environmental Sustainability: Many injection molded components can be made from recycled materials, and the process itself generates minimal waste.
The Injection Molding Process
Key Stages of Injection Molding
The injection molding process consists of several key stages:
- Material Preparation: Raw plastic pellets are fed into a hopper and heated until they melt into a viscous liquid.
- Injection: The molten material is injected under pressure into a pre-heated mold cavity.
- Cooling: The material is allowed to cool and solidify, taking the shape of the mold.
- Ejection: Once cooled, the finished part is ejected from the mold, and the process begins again with a new cycle.
Materials Used for Injection Molded Parts
Various materials can be utilized for injection molded parts, including:
- Thermoplastics: Widely used due to their versatility, recyclability, and ability to be remolded such as ABS, polycarbonate, or polypropylene.
- Thermosetting Plastics: These materials harden permanently once set, making them ideal for applications requiring high durability and heat resistance.
- Elastomers: Used for flexible parts like gaskets and seals.
- Metals and Alloys: Though less common, specialized processes exist for injecting metals into molds for parts requiring exceptional strength and heat resistance.
Common Challenges in the Injection Molding Process
While injection molding is a powerful manufacturing technique, it is not without its challenges:
- Material Costs: High-quality materials can significantly impact overall production costs.
- Mold Design and Maintenance: Molds must be expertly designed to avoid defects; poor design can lead to costly rework and maintenance.
- Production Waste: Excess material can lead to waste issues, necessitating careful material management.
- Cooling Time: Extended cooling times can slow production, requiring optimization of the cooling design.
Designing Effective Injection Molded Parts
Best Practices for Part Design
To achieve successful injection molded parts, designers should adhere to certain best practices:
- Draft Angles: Implement adequate angles on vertical surfaces to facilitate part ejection.
- Wall Thickness: Maintain uniform wall thickness to avoid warping and uneven cooling.
- Fillets and Radii: Incorporate rounded edges to strengthen the parts and improve flow during injection.
Common Design Flaws to Avoid
While designing, avoid these common pitfalls which can lead to poor performance:
- Inconsistent Thickness: Variations in wall thickness can cause warping and stress concentrations.
- Poor Venting: Inadequate vents can lead to trapped air pockets, causing defects.
- Overly Complex Designs: While complexity can be beneficial, overly intricate parts can increase manufacturing time and costs.
Iterating on Designs for Production
Iterative design is crucial in refining injection molded parts:
- Prototyping: Create prototypes to assess designs and test functionality before full-scale production.
- Feedback Loops: Incorporate input from production teams and end-users to enhance designs continuously.
- DFM (Design for Manufacturability): Collaborate closely with manufacturing engineers to ensure designs are practical and cost-effective.
Applications of Injection Molded Parts
Industries Utilizing Injection Molding
Injection molded parts find applications across diverse industries:
- Automotive: Components like dashboards, switches, and panels are commonly produced using injection molding.
- Consumer Electronics: From casings to intricate designs inside devices, injection molds create lightweight, durable components.
- Medical: Medical devices and components requiring precision fit are frequently produced using injection molds.
- Packaging: Many packaging products, including containers and closures, leverage injection molding for efficient and effective solutions.
Everyday Products Made from Injection Molded Parts
Countless everyday items are produced through injection molding:
- Plastic bottles and bottle caps
- Toys, including building blocks and figurines
- Household goods like furniture and storage bins
- Automotive parts, including bumpers and interior components
Future Trends in Injection Molded Part Applications
The future of injection molded parts looks promising with several trends emerging:
- Sustainability: Growing demand for biodegradable and recycled materials is shaping future designs.
- Smart Products: The incorporation of IoT technology into injection molded parts for enhanced functionality.
- 3D Printing Integration: Combining traditional injection molding with 3D printing technologies to create custom molds and parts efficiently.
Conclusion and Resources
Recap of Injection Molded Parts
Injection molded parts play a critical role in modern manufacturing, providing businesses with versatile, efficient, and high-quality solutions. Understanding the complexities of the injection molding process and the best practices for designing parts can lead to successful outcomes.
Additional Learning Resources
For those looking to further their knowledge on injection molding, consider the following resources:
- Injection Molding Basics by Protolabs
- Injection Molding Guide by 3D Hubs
- Xometry’s Injection Molding Resources
Contacting Experts for Custom Injection Molded Parts
If you are looking to procure injection molded parts tailored to your specific needs, it’s advisable to consult industry experts. They can provide insights into material selection, mold design, and production processes that will effectively meet your requirements.